Board design, cycle time, and coating flow can all impact a designer’s path to a successful coating process, so what are the key factors to bear in mind to achieve the best outcomes for your coating processes? In this column, I’ll be highlighting some of the key challenges and commonly asked questions about conformal coatings that every Design Engineer should take into consideration when specifying the coating process. As assemblies become ever more densely populated, and housing /casing designs become more permeable to save weight, the use of conformal coatings is becoming essential to protect the assembly from its operating environment and ensure acceptable reliability for the application intended, especially when operating in hostile environments. Let’s explore some of the key factors that will help follow our five-point.
Coating Thickness
When specifying the thickness of the coating on an engineering drawing, the industry practice is to measure coating on a flat, unencumbered area of the assembly, and not on items like component leads. As many modern assemblies are very component-dense, it is often difficult to find a flat, unencumbered area of the assembly. Consequently, it is a common and accepted practice to use witness or process control coupons for such measurement.
Designers will need to know that the ‘nominal thickness’ measured on flat, unencumbered areas or witness coupons will have no relation to the thickness of coating achieved on the corner of a discrete, or the leads of ICs, where thickness might be in the order of 1 micron or less, with a nominal thickness of 25 or 50 microns. In a recent study, performed by the IPC, ‘Conformal Coating – State of the Industry’ there were some very eye-opening results for many folks who assumed they were getting 25 microns everywhere.
Again, the key takeaway is nominal coating thickness is a process indicator only, the actual coverage on leads and components is far more important to the reliability of the assembly and this should be understood by all parties. The goal is the greatest degree of coverage possible, and cross-sections should be performed to understand how the application process is delivering this critical to success parameter. The witness coupon will only tell you if your process has changed significantly.
The Importance of Coating Cycle
The coating cycle time is a critical requirement in lean manufacturing to ensure the production takt time can be met to maintain a balanced production line. It is advantageous for the coating cycle time to be as fast as possible to ensure any accumulated production can be cleared as rapidly as possible, should any previous operations suffer a stoppage.
If we look at a selective coating machine as an example, depositing stripes of coating material that can be programmed to stop and start on demand. The coating stripes can be deposited to create a pattern, avoiding areas such as switches, connectors, and test points that must not be coated to prevent interference with form, fit, or function. The coating stripes deposited are usually in the 8-15mm range, for optimum accuracy and minimizing overspray and splashing. When the area to be coated is less than 8mm in width, then it is necessary to utilize a dispensing step, which is a cycle time killer. Due to the combination of machine X/Y positional accuracy, material fluid dynamics, and component topography, 2-3mm is usually as close to keeping out areas as anyone would be the comfortable coating for a repeatable process. So must coat and keep-out areas within 2-3 mm of each other present a problem and again dispensing will be required, another process step which kills cycle time.
Impact of board design on the coating process
The board’s design can have a significant impact on the success of a coating operation by influencing which methods can be used and determining what degree of coverage can be achieved within a required cycle time. In general, the fewer areas there are on a board that must be free from the coating, the faster the coating cycle time will be. Should the coating cycle time be too long, then a decision can be made to either determine the most vulnerable parts of the assembly and focus on that area in the available cycle time, or to split the coating across several workstations.
Designers should be aware that coating the edges of assembly is not considered value added for most applications. Most design standards do not allow inner layer circuit traces to be closer than 0.63 mm from the edge of the board. The act of routing the board edges results in smearing the epoxy resin over the cut glass fibres or the reinforcement material, sealing off the inner layers. A designer might specify coating board edges where such sealing does not occur, such as with V-scored, punched, or sheared edges.
One area where designers can really help production is to specify where coatings are optional or “don’t care” in the engineering drawing. It is best practice to specify the areas that need to be coated and the areas that don’t as well as the ‘don’t care areas to help the coating process run as smoothly as possible.
Another helpful tactic is placing connectors and components that must not be coated along one edge of the assembly to simplify the conformal coating application process. This may allow dip coating to be explored as a potential alternative methodology, speeding up application times and reducing costs. Also, avoid large arrays of discrete components, which can pose a huge coating challenge due to the high levels of capillary forces present. The net result is often areas of no coverage/protection on the board as well as areas of excessive thickness prone to stress-cracking, de-lamination and other coating defects. Similarly, tall components present challenges of their own by the creation of shadowed or hard-to-reach areas. Splashing is another associated problem. The trick is to avoid placing tall components next to ‘must-coat’ components in order to avoid this eventuality.
Improving Coating Flow
For many coatings, it is difficult to limit the flow of coating from the application site to adjacent sites as the coating will have some level of capillary flow (often referred to as wicking), taking the coating to unanticipated areas. This brings us back to the importance of avoiding putting components with MUST NOT be coated close to components which MUST be coated. Placing a keep-out zone at the base of a tall component, such as an electrolytic capacitor, will create a lot of problems in manufacturing as the coating flows down the tall part into the keep-out zone.
Coating flow is also important on low standoff devices, such as BGAs or CSPs, which may have microvias under them. The coating can wick under the parts and down the vias to the opposite side of the assembly. To avoid this problem, the vias under low standoff components can be tented with a solder mask or have the vias filled with solder or suitable via-fill material. In addition, the presence of conformal coating beneath BGAs for example can significantly reduce the reliability of the solder joints. The coating process should be designed to aim to minimize coating flow beneath BGAs or use an Underfill material to improve the mechanical reliability of these devices.
What other processes can impact the coating?
Flux residues from ‘no-clean’ solder pastes and selective soldering or wave soldering can significantly impact the ability of the coating to adhere and perform its function of protecting the assembly. Compatibility studies should always be performed prior to the implementation of coating over a ‘no-clean’ process and care must be taken to ensure the soldering processes remain under tight controls.
The designer should ideally be aware of what kinds of manufacturing practices may occur following the application and cure of the coating, as other materials such as thermal greases/putties and rework/repair chemicals, can all have an impact on the integrity and overall performance of a coating. Also, when selecting adhesives for assemblies, care should always be taken to ensure that they are compatible with the selected coating materials and processes. Adhesives that are not compatible can have a detrimental effect on the overall performance of the coating.
Having started about the importance of making sound early-stage design decisions, it is important to understand “what effects what” on the surface of the board to ensure the successful conformal coating is achieved. Implementing these lessons will prevent potential production disasters not only with conformal coatings but also in other areas of production as well. Look out for my next column where I will be covering more coating tips and tricks.
Authored Article by:
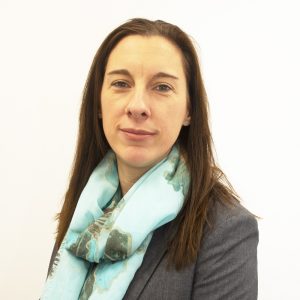